Closing the Gap

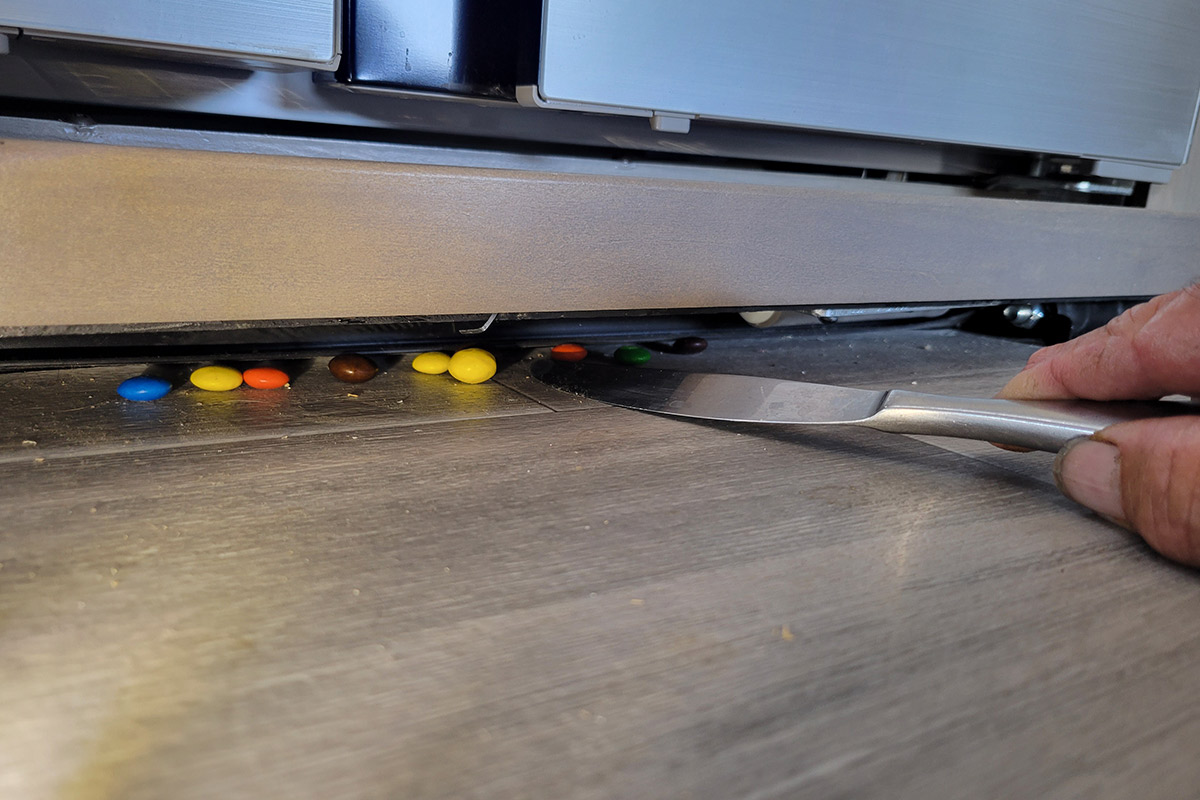
It’s just not a good scene, and likely attracts bugs and mice looking for some nutrition. I needed a solution.
Since the gap is more than an inch high, there’s plenty of space for just about anything that falls on the floor to take sanctuary. I turned to Amazon and while surfing different types of seals I ran across a garage-door seal that looked promising. What I was looking for needed to be long enough to attach to the front of the slideout lip and reach the floor — and not look like an afterthought. Fortunately, the “garage seal” I found — “Garage Door Top & Sides Seal 32.8 feet, Weatherproofing” (Amazon, $10.47 for a 32.8-foot roll) fits the bill.
The second part of the project — ever notice there is always a “second part” to what seems to be a simple project? — was to find an adequate step-down molding to provide a finished look of the seal. Since the slideout is exactly 14 feet long, it took two 10-foot lengths of “Floor Transition Strip Self Adhesive, PVC Carpet to Tile” step-down molding (also procured on Amazon; $18.99 for each length). The PVC, Gray Grain Wood molding I selected was almost an exact color match; other colors are also available.
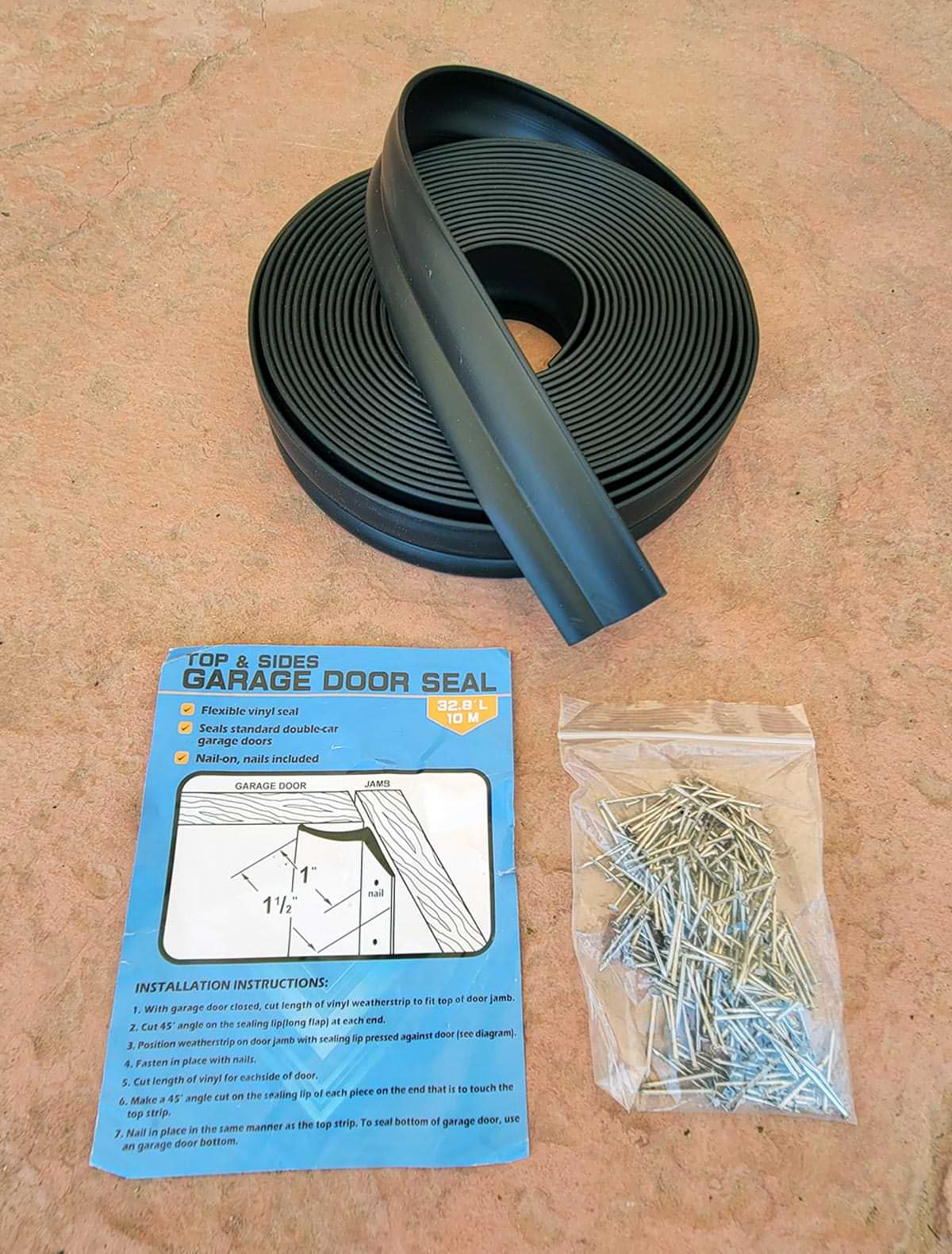
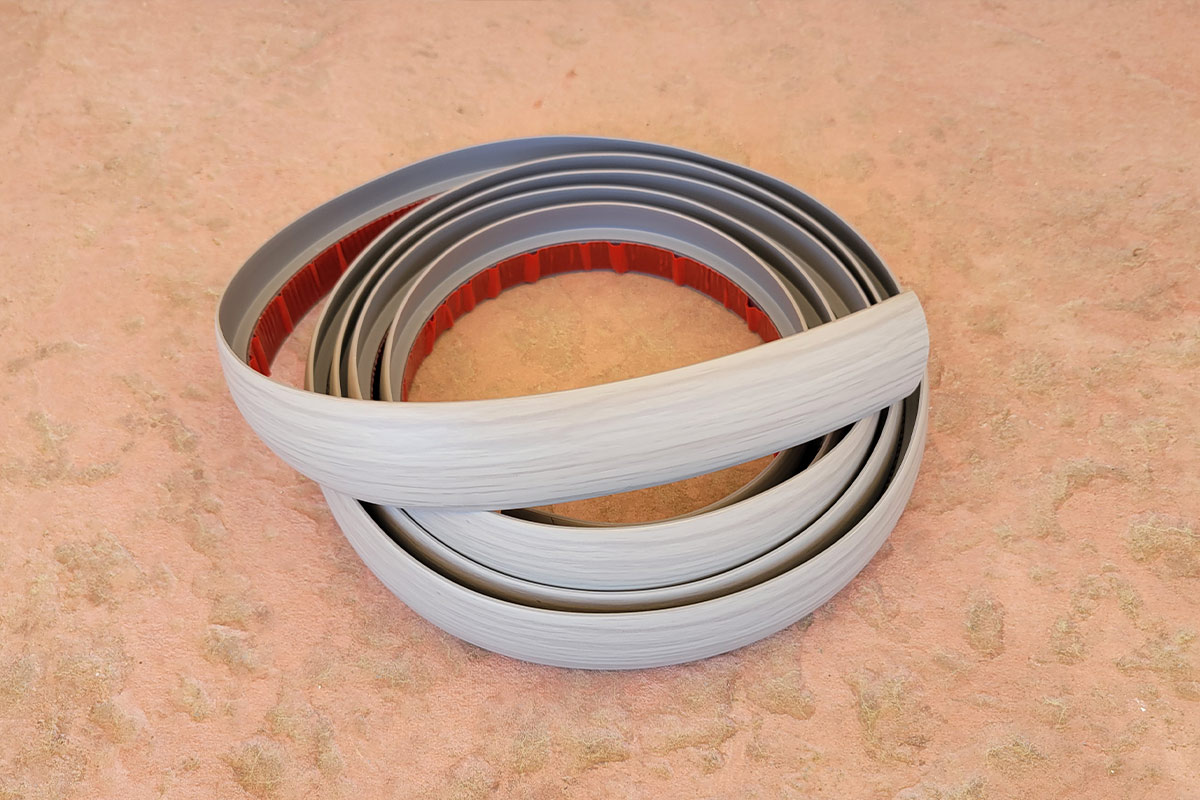
The “secret” to installing the products, as I soon realized, was to install the garage-door seal so it just barely touches the floor. There’s always going to be some flexing and movement as a slideout goes in and out, and it does not need to sweep the floor like a wiper blade — it just needs to prevent items from being lodged under the slideout floor.
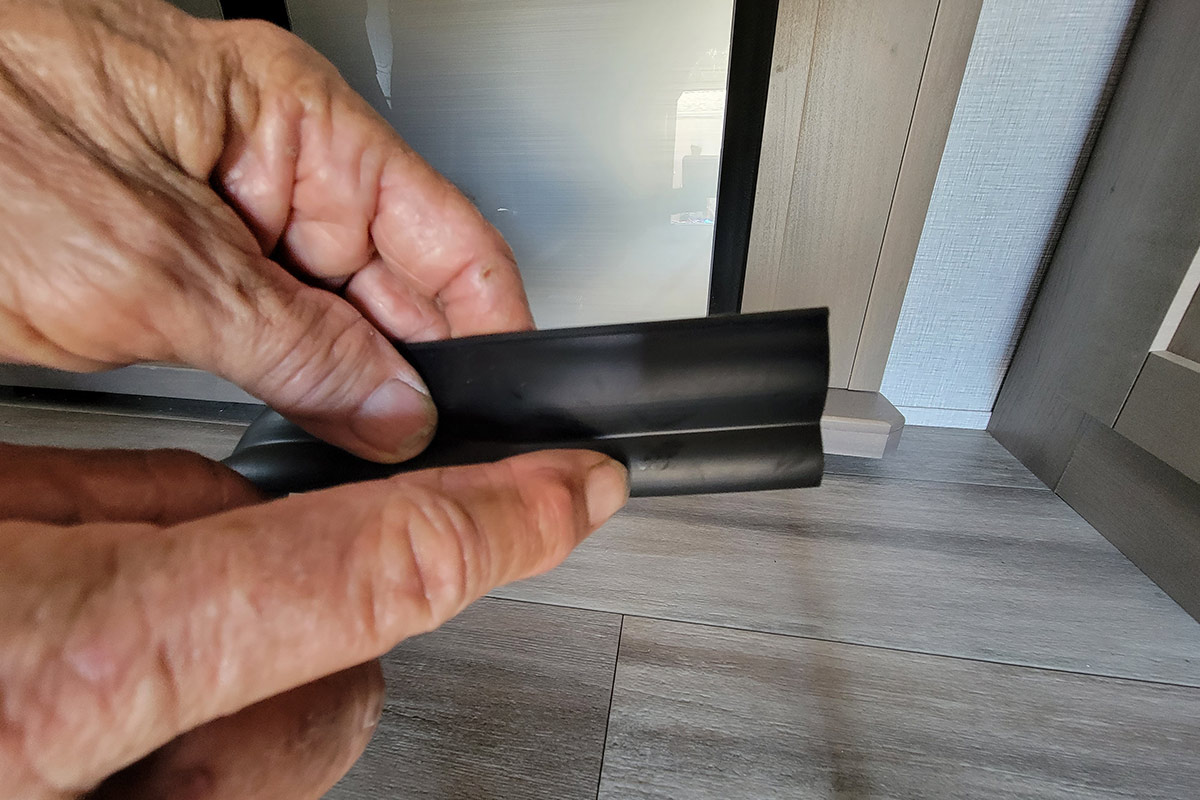
I started at one end and drilled the first pilot hole through the seal and front lip of the slideout, then drove in a nail. From there, the other pilot hole locations were marked with 6-inch spacing and drilled one at a time, and each nail was set. I was hoping that I could make the turn around the edge of the slideout ledge, but that didn’t work because the lip on the side of that curve was too narrow to set a nail. In the end, it was a straight run. The nails have a small flat head on them, so I decided not to pound them into the seal too hard for fear of cutting through the seal.
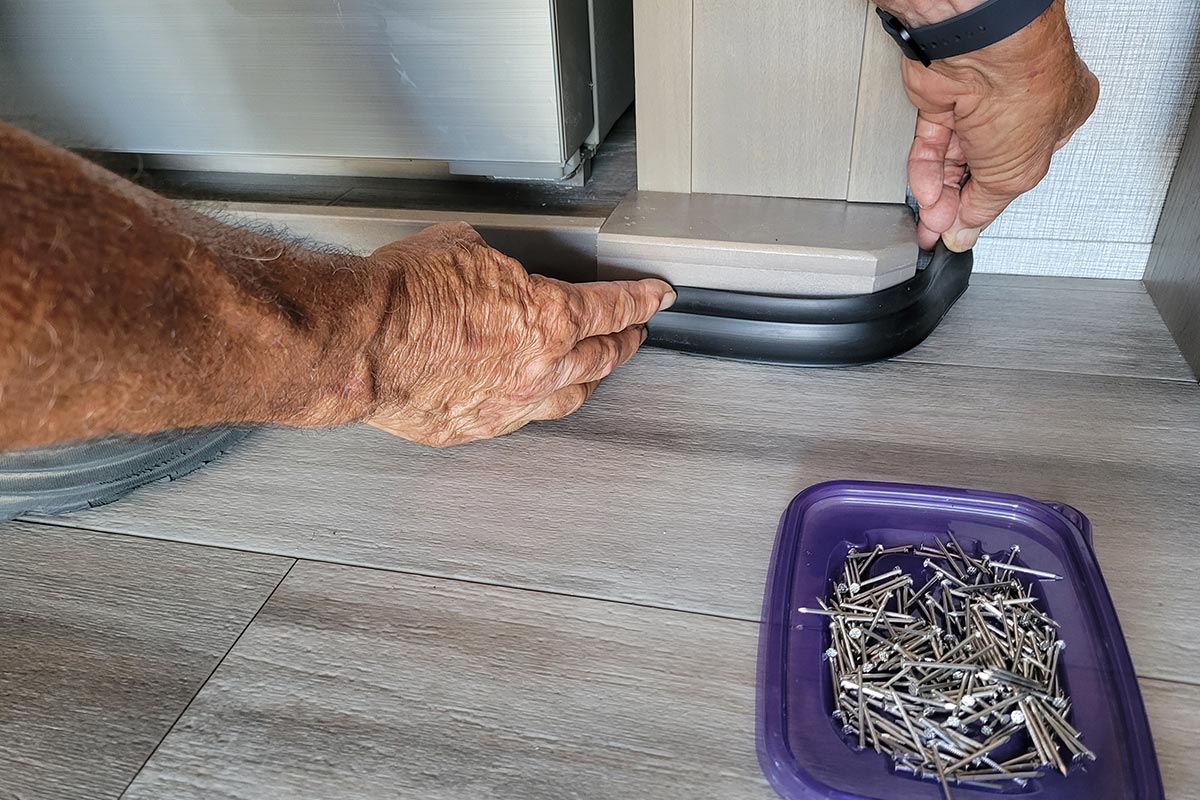
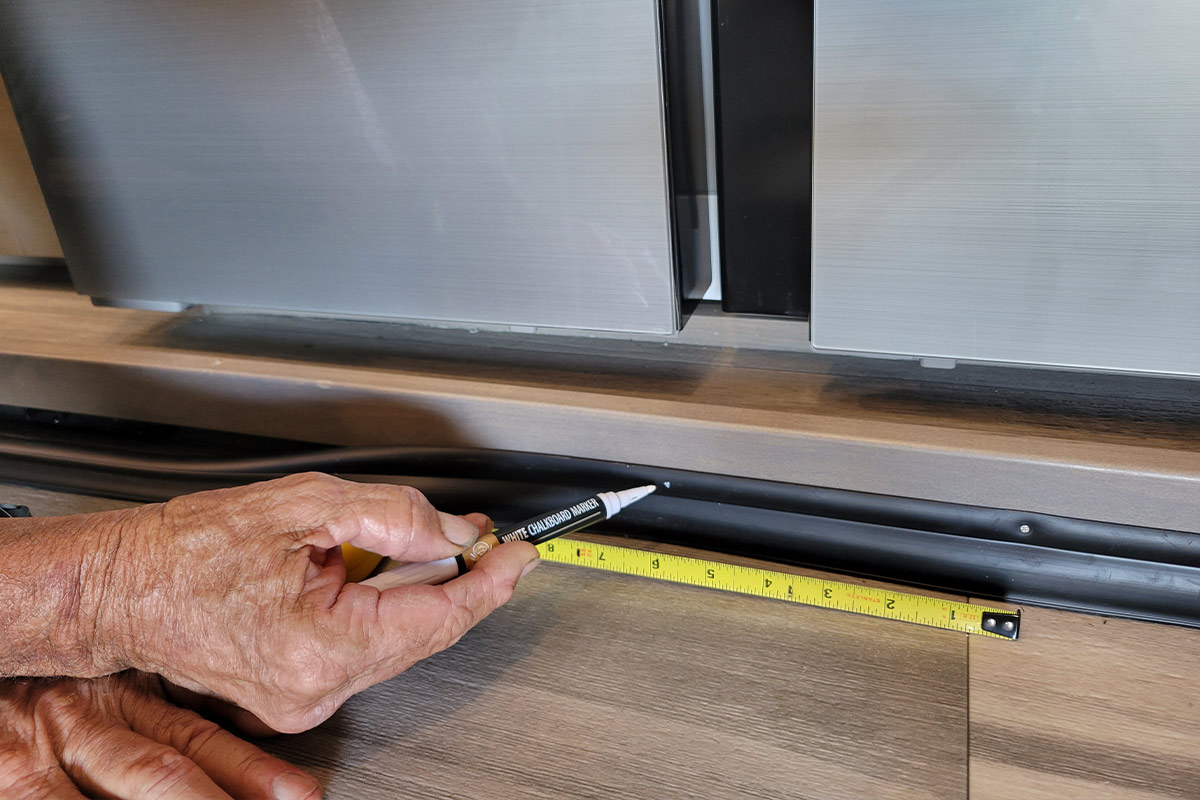
Satisfied that the seal was in place, I used a paper towel and alcohol to clean the entire length of where the molding — which has strong double-sided tape for adhesion — was to be applied. I set the lip of the molding right on top of the rubber seal, which gave me a gauge between the top of the seal and the top of the lip for making a nice straight line all the way across the slideout. The tape stuck better than I thought it would; if it starts to come loose down the road, beige-colored brad nails can be driven through the molding into the slideout floor facing.
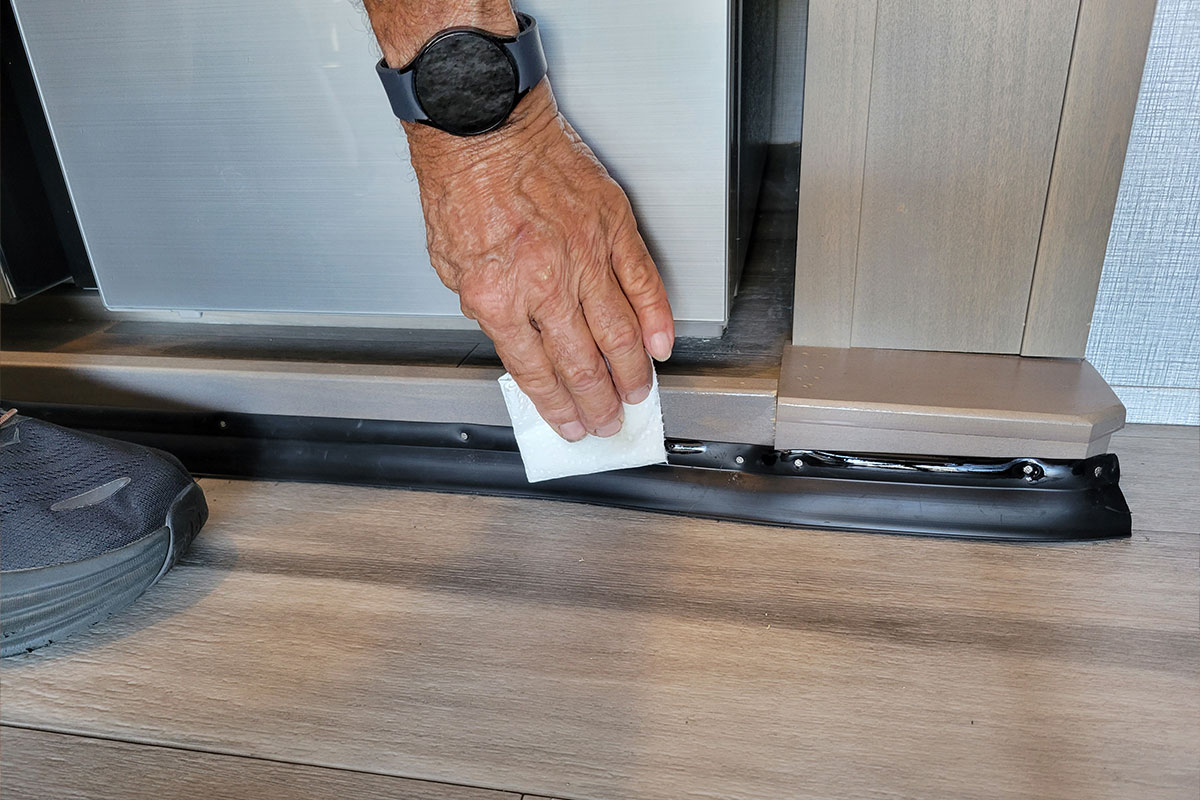
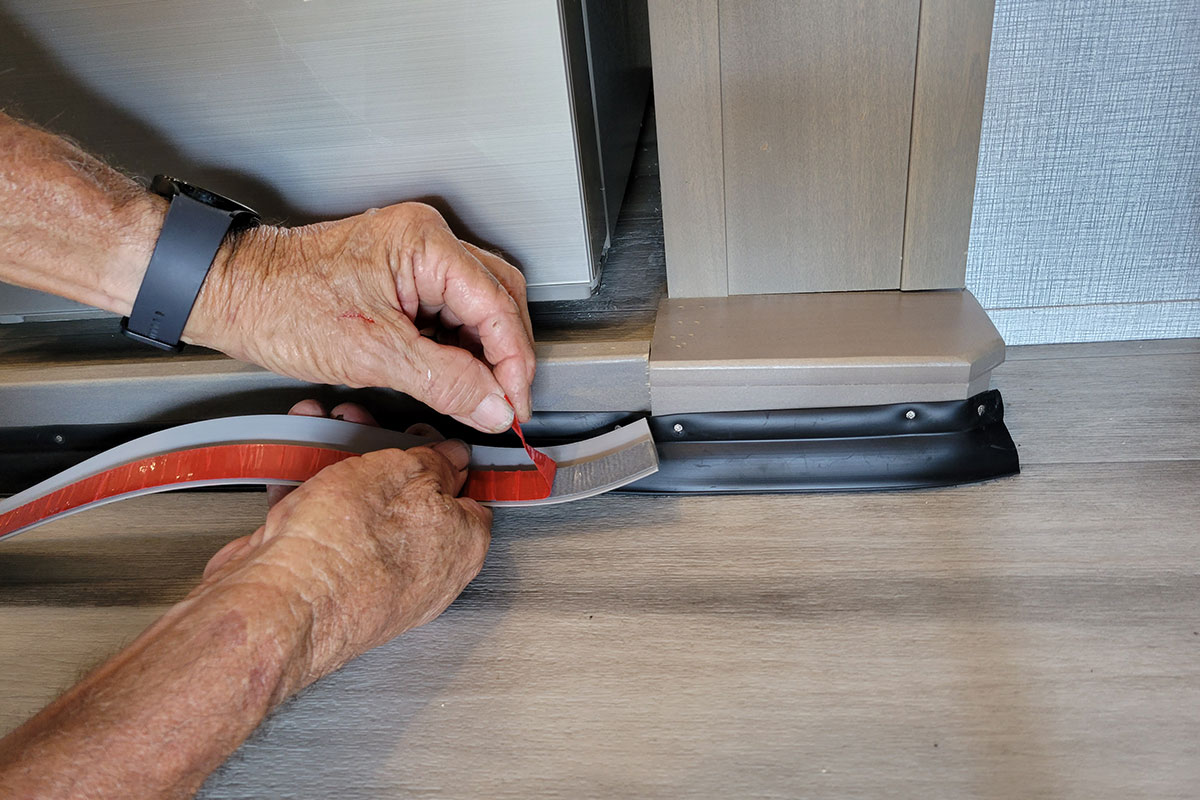
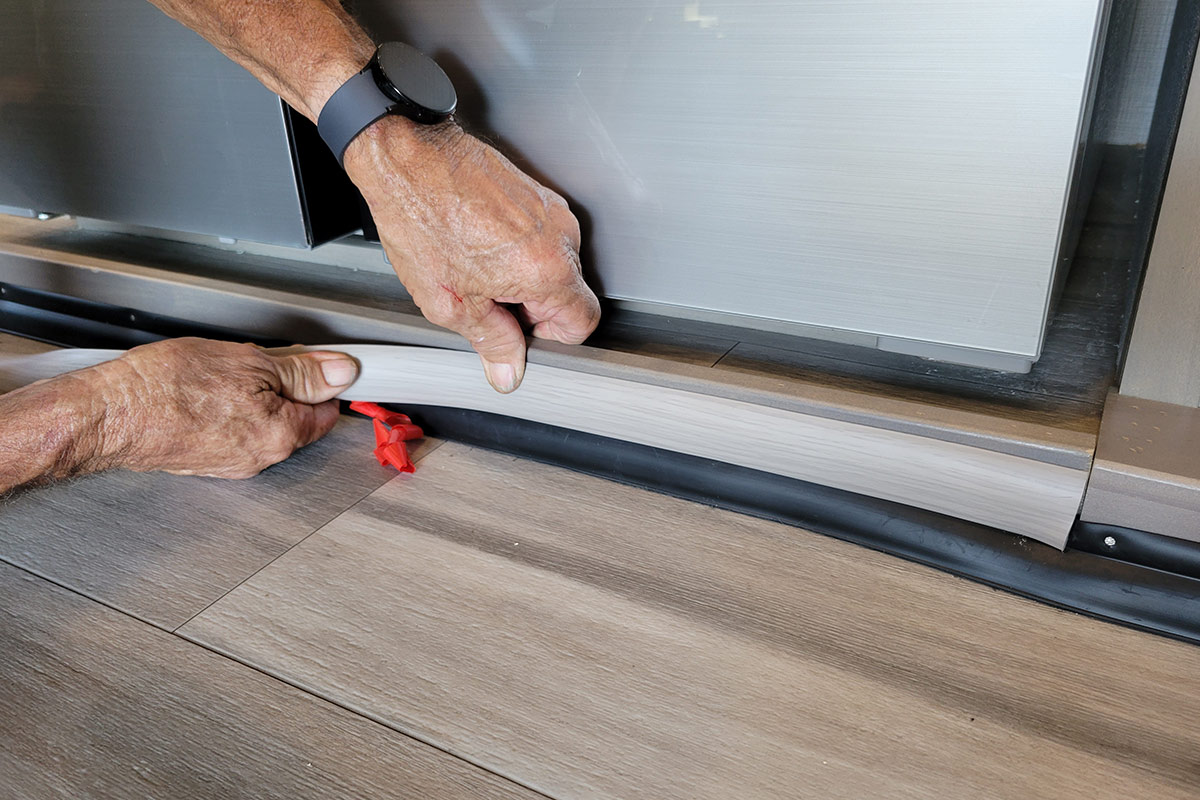
Granted, I was a little worried about how the black seal would look hanging down from the slideout floor, but it actually looks like it was factory-installed — and even matches the black fireplace and oven. When the slideout moves in and out, the new seal follows the slideout pathway nicely and remains straight when the room is extended fully — and finally closes the gap to dropped items.
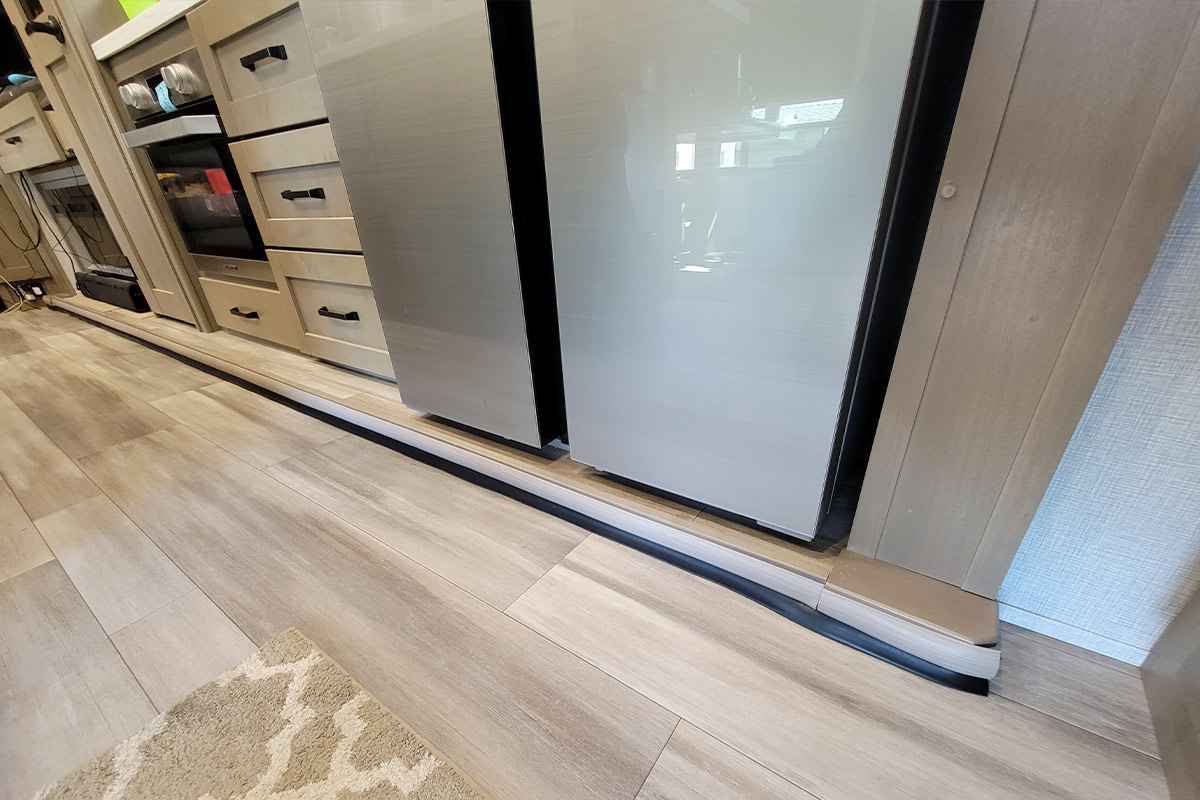
Already a Subscriber? Click here for Access to the Full Issues.